Evening all,
I’m after some help with a garden room construction. I suspect the standard of this build is far below what many of you are accustomed to, but please bear with me because I need to salvage what is currently there and try to make the best of it. In this post I’ll mainly let the pictures do the talking, so it might get a bit image heavy.
This is it as it stands as of now:
Originally there was a brick shed here, circa mid-century. Then in the late 80’s or so that was replaced by a blockwork shed on the same plot.
As you can see this structure was well past it’s prime, so a month ago I had it knocked down and the new timber structure erected in its place. I mention this because no additional ground work has been done; the timber frame has simply been put up on the footprint of the previous shed, which I presume had rudimentary concrete footings or plinth.
The firm I had do the work cleared the site while I was away and put the frame up before I was back so I never got a chance to inspect the rear walls or ground, both of which are uneven and have some cracks.
They builders have now abandoned work and left me to it and I have these main problems to address:
1 - The roof is leaking, and the flashing at the rear wall is appalling.
2 - The pre-existing concrete base, which is the floor of the current room, is uneven with a 6cm discrepancy in heights.
3 - Doors and windows need to be measured up and installed
4 - The OSB is left unclad in places, and seems to be interior grade OSB anyway.
5 - The wiring is behind plaster and unlabelled so will need to be identified.
1 The builder laid 50 or 60cm rolls of CORTEX EPDM membrane system by OBEX UK. It's used for lining frames, etc, not roofs. The primary advantage of EPDM for flat roofs is that it can be laid in one sheet with no seams or join. This mess is full of creases, wrinkles, unsealed overlaps and the rear is just loosely laid on lead flashing. It’s not even bonded down, so rain is streaming through the roof.
What I need to know is the simplest way to weatherproof this. I thought I might just be able to overlay it with a single sheet of proper epdm, but I believe it doesn’t bond to itself, or is not recommended, so I have to explore other options. Maybe tape to bond down all the seams. Probably redo the flashing so the rubber is chased into the wall behind. Perhaps it’s possible to just physically secure a sheet of epdm over the whole roof and just pin it all the way around the fascia without necessarily bonding it down? Failing that I would just be forced to rip it up and do the whole thing again. Potentially difficult, messy and more expensive. Or I could maybe over board it and do a new roof with better pitch?
I’m after some help with a garden room construction. I suspect the standard of this build is far below what many of you are accustomed to, but please bear with me because I need to salvage what is currently there and try to make the best of it. In this post I’ll mainly let the pictures do the talking, so it might get a bit image heavy.
This is it as it stands as of now:
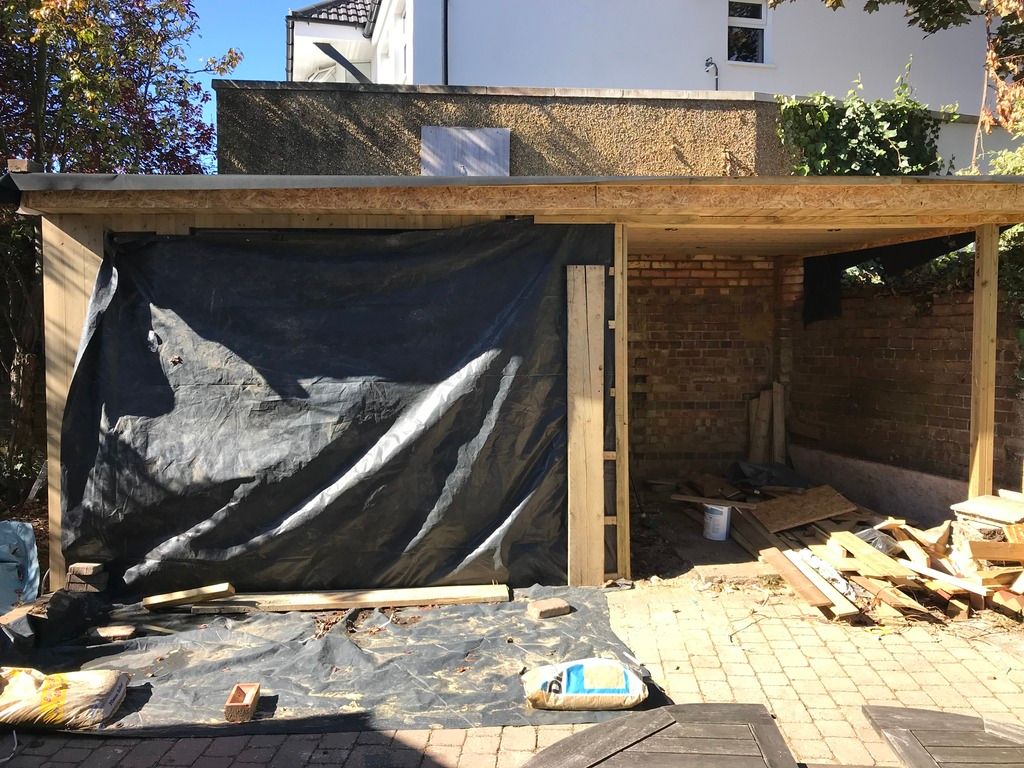
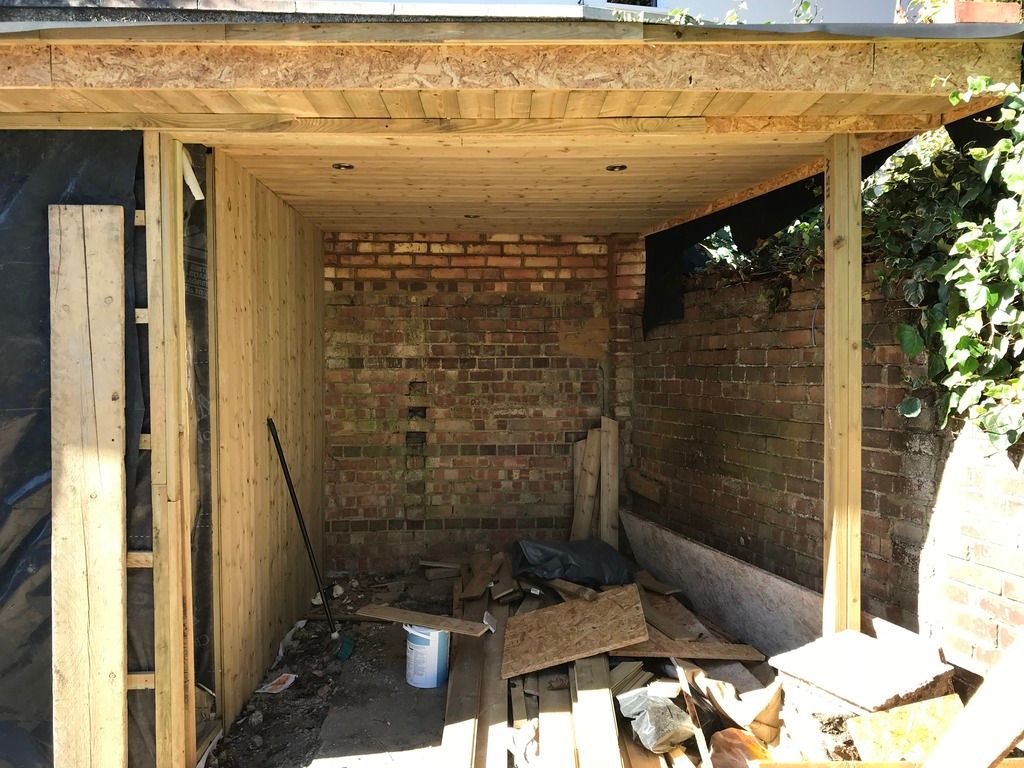
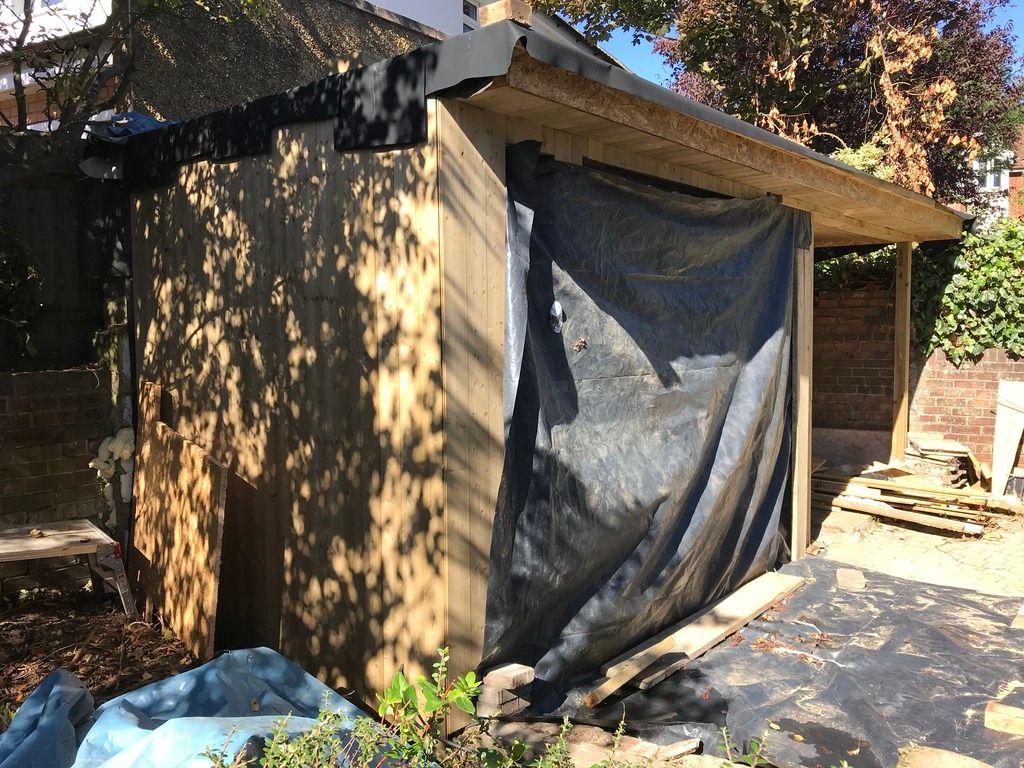
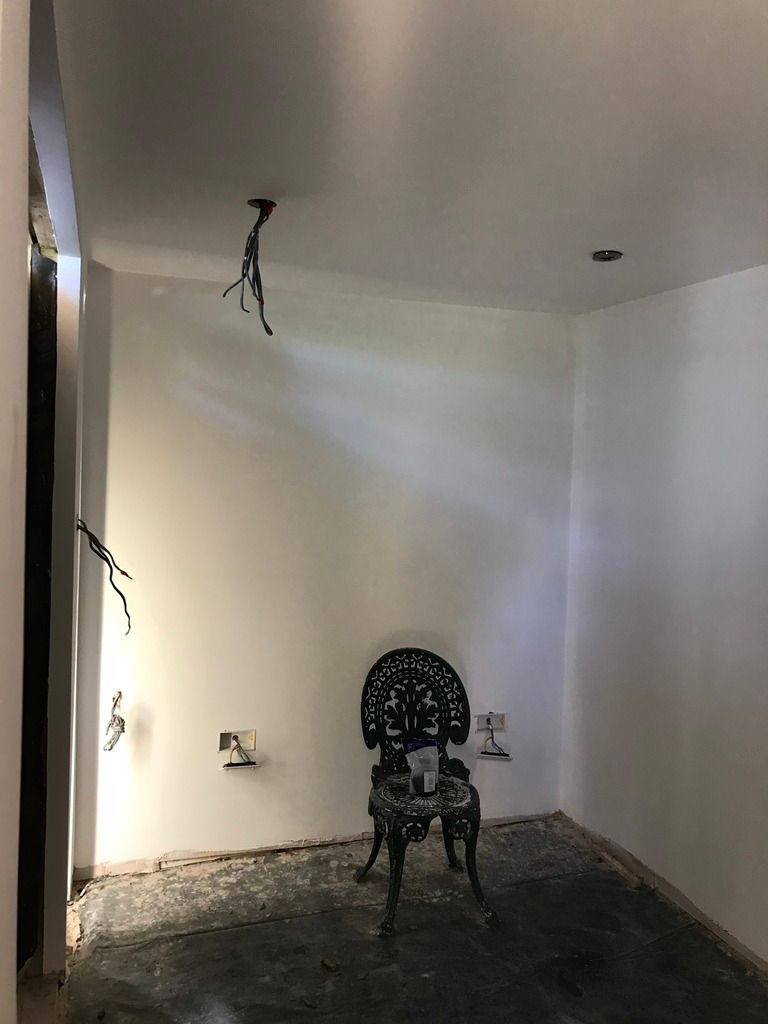
Originally there was a brick shed here, circa mid-century. Then in the late 80’s or so that was replaced by a blockwork shed on the same plot.
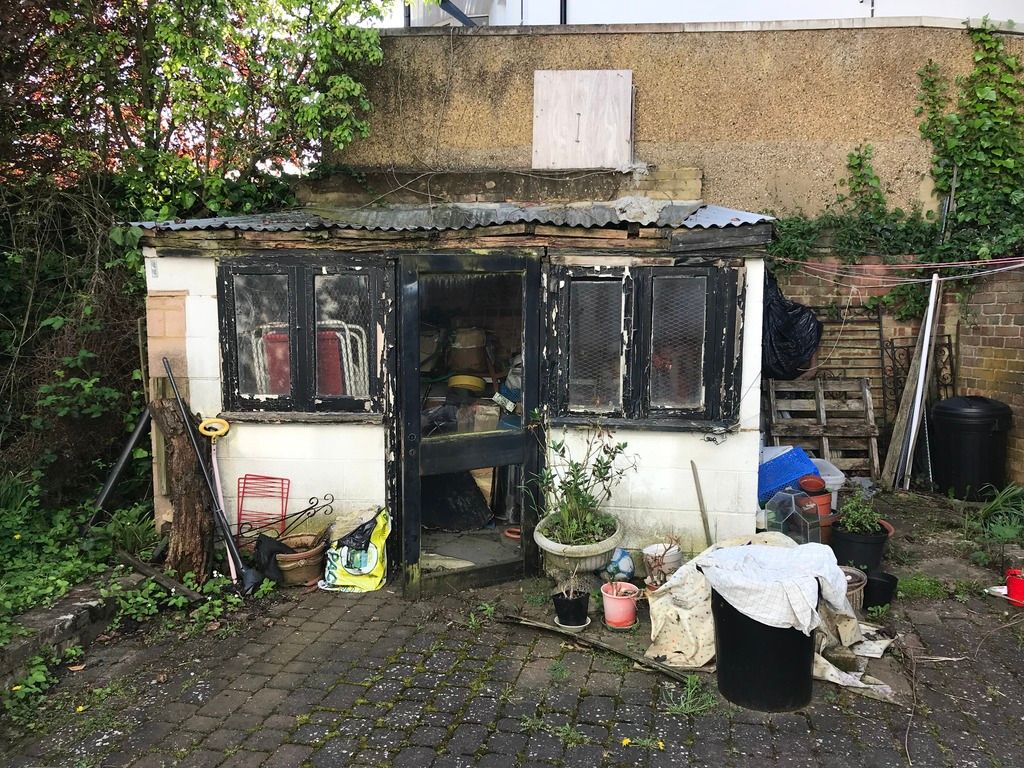
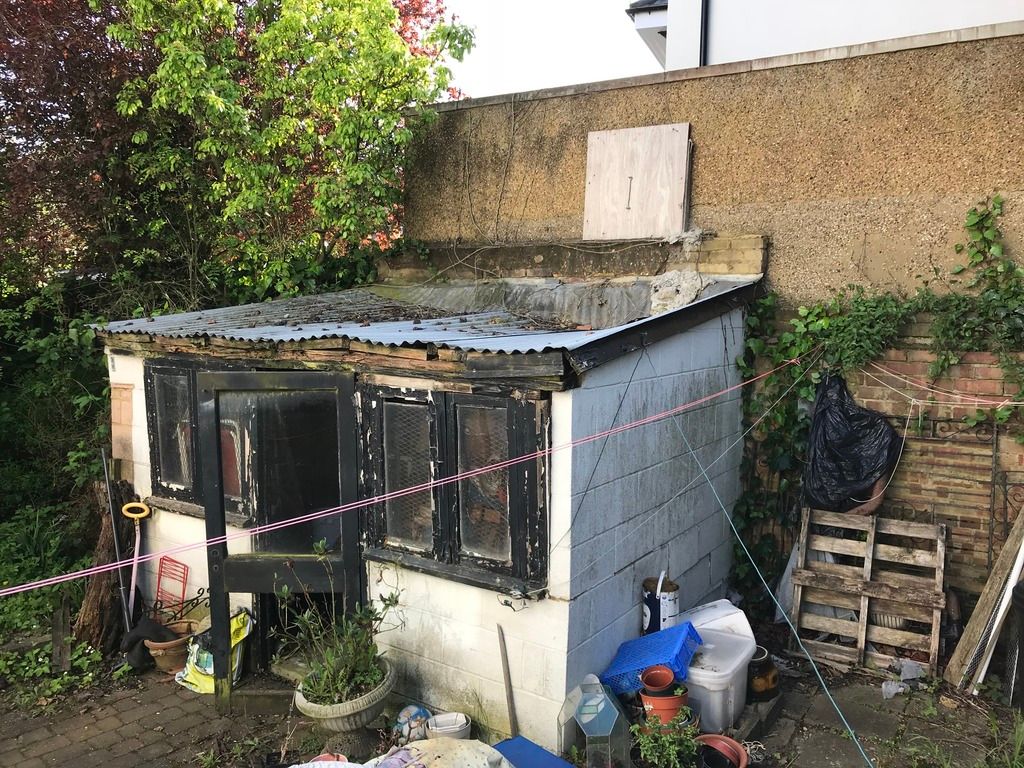
As you can see this structure was well past it’s prime, so a month ago I had it knocked down and the new timber structure erected in its place. I mention this because no additional ground work has been done; the timber frame has simply been put up on the footprint of the previous shed, which I presume had rudimentary concrete footings or plinth.
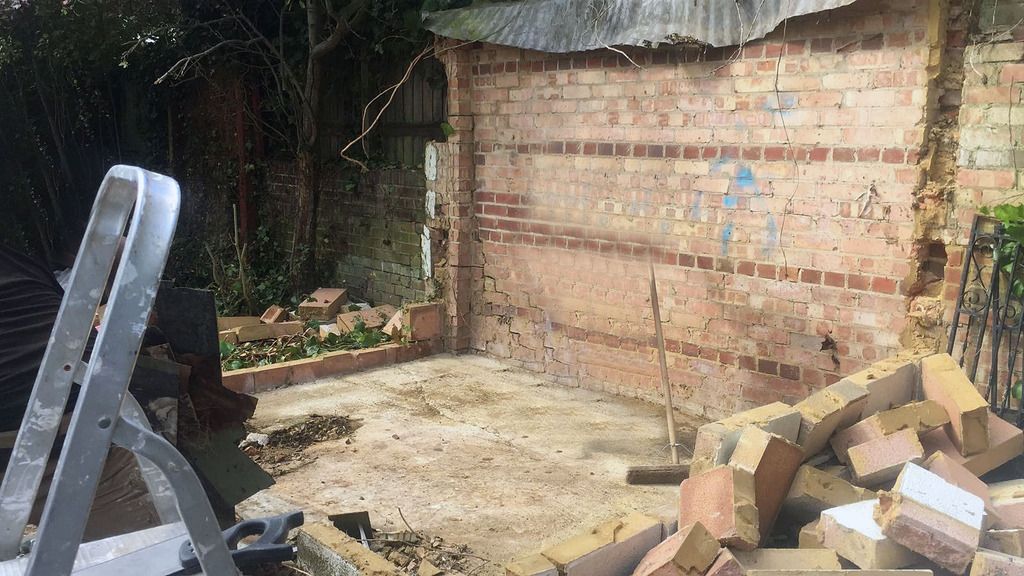
The firm I had do the work cleared the site while I was away and put the frame up before I was back so I never got a chance to inspect the rear walls or ground, both of which are uneven and have some cracks.
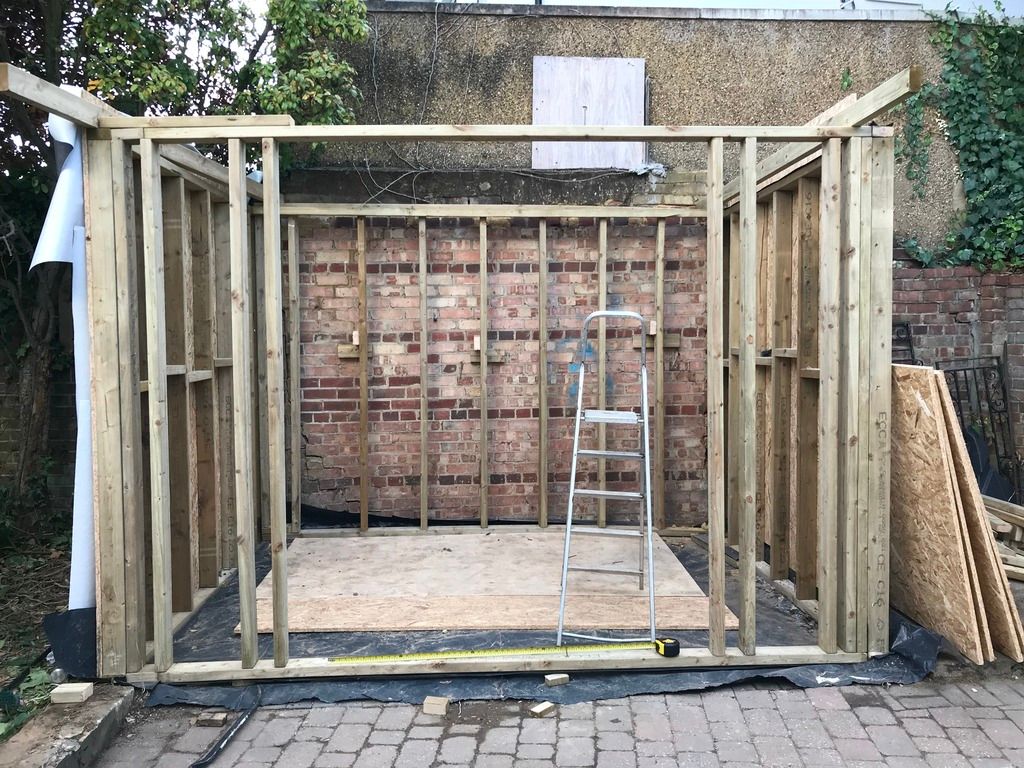
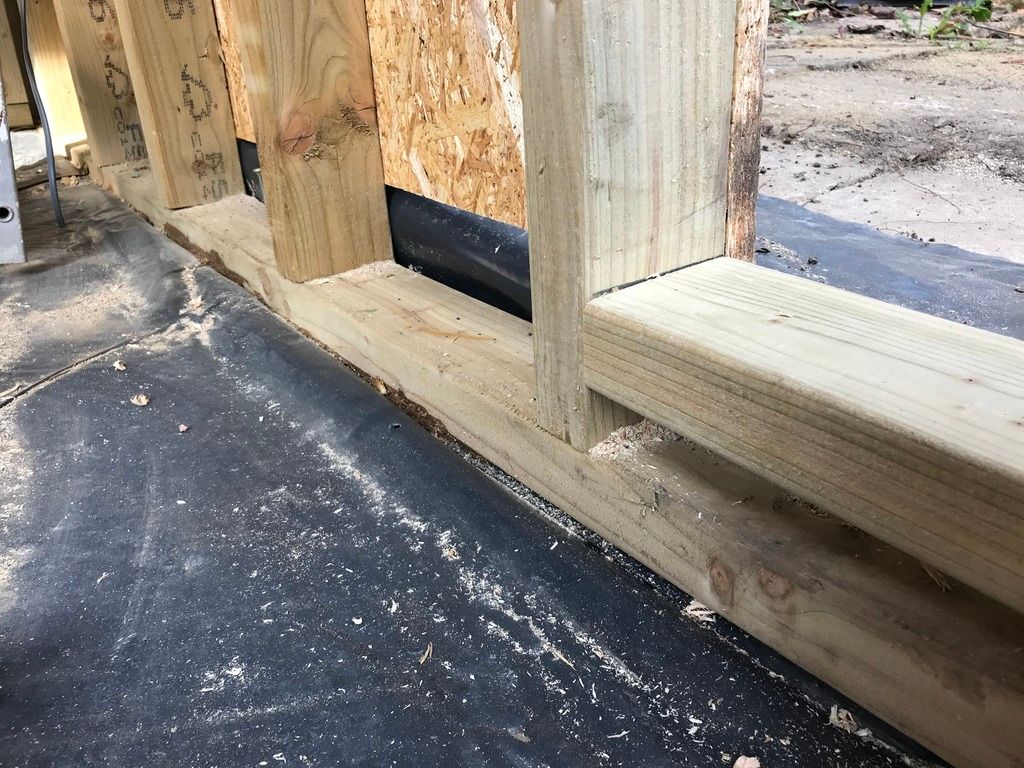
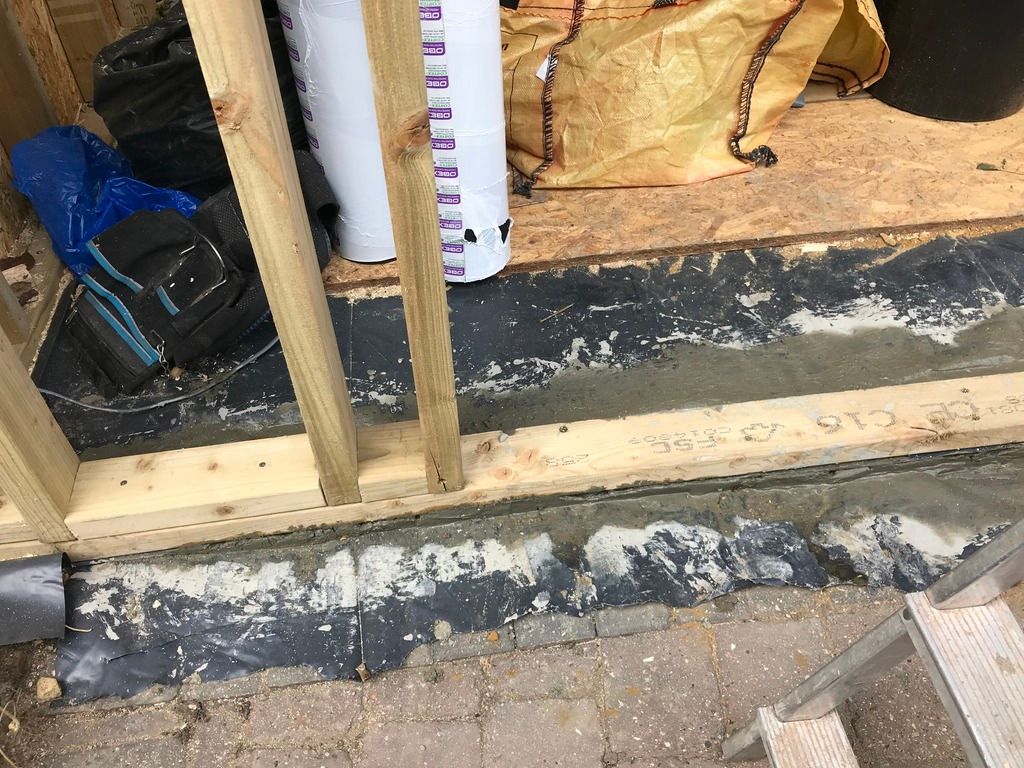
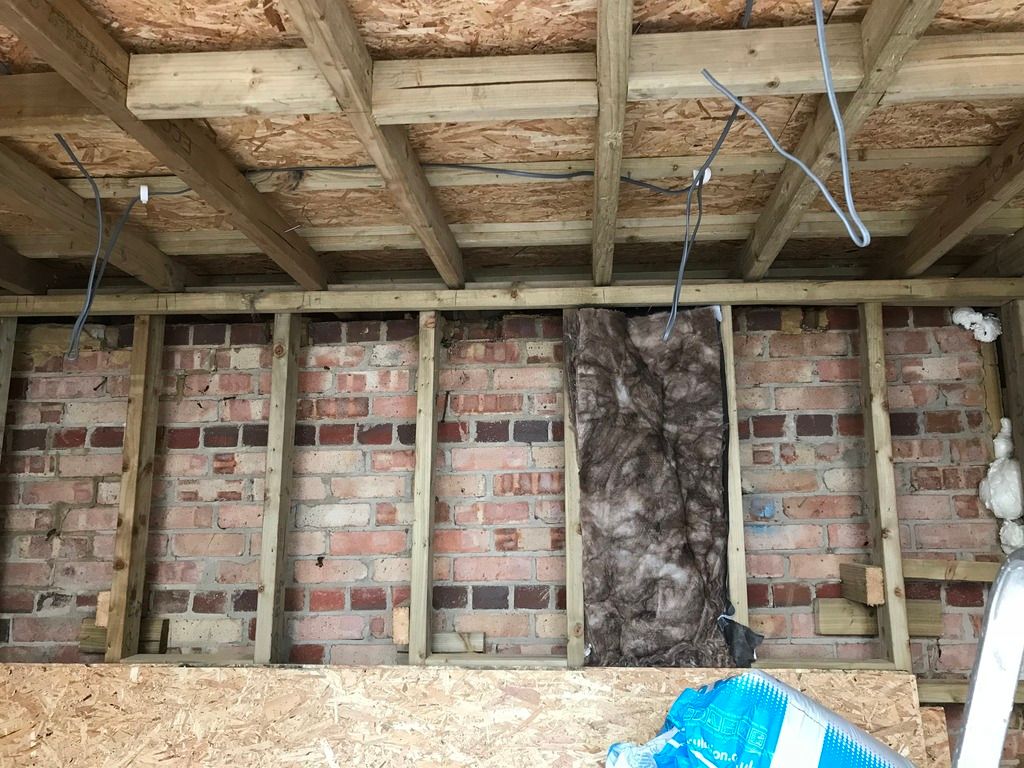
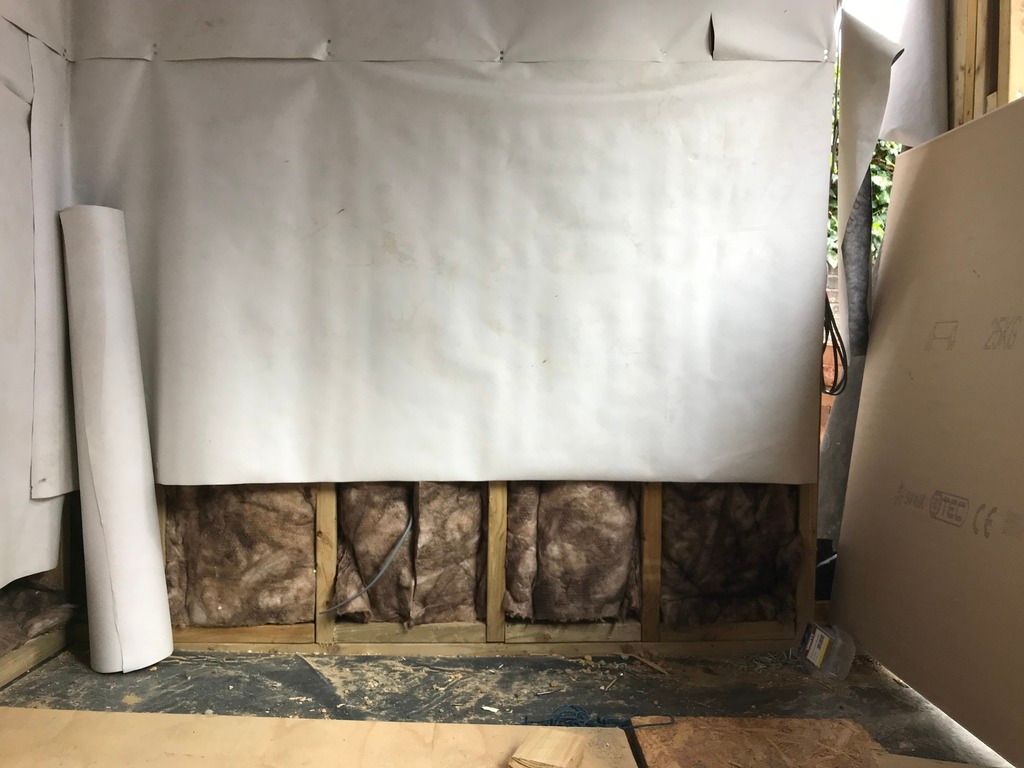
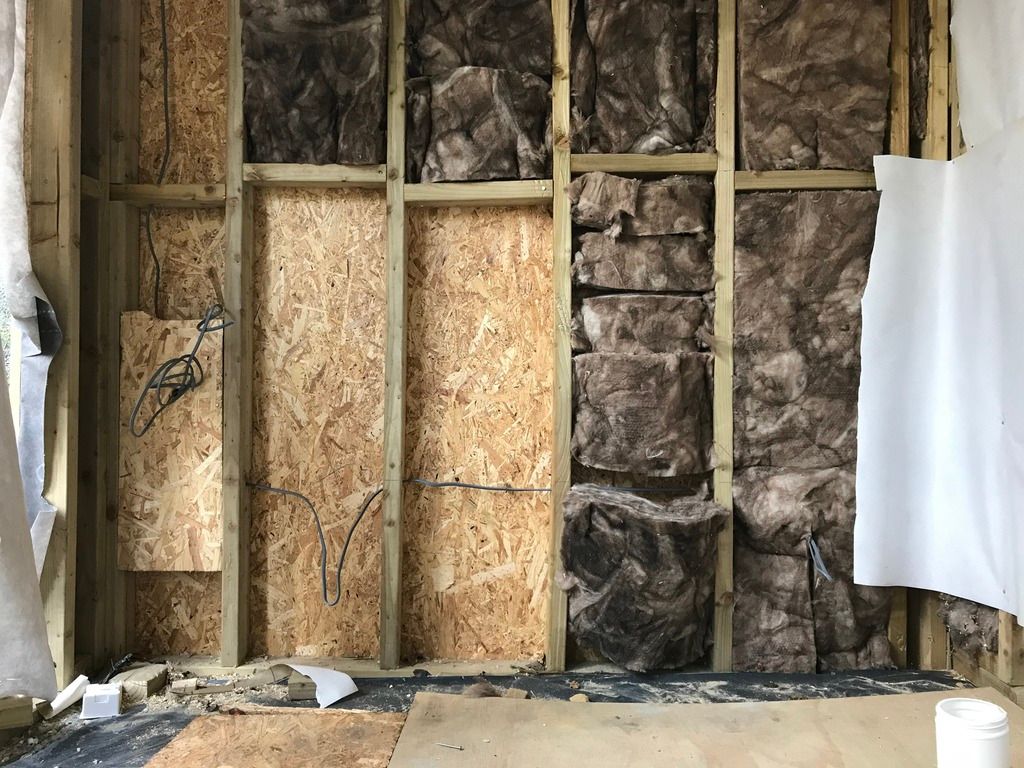
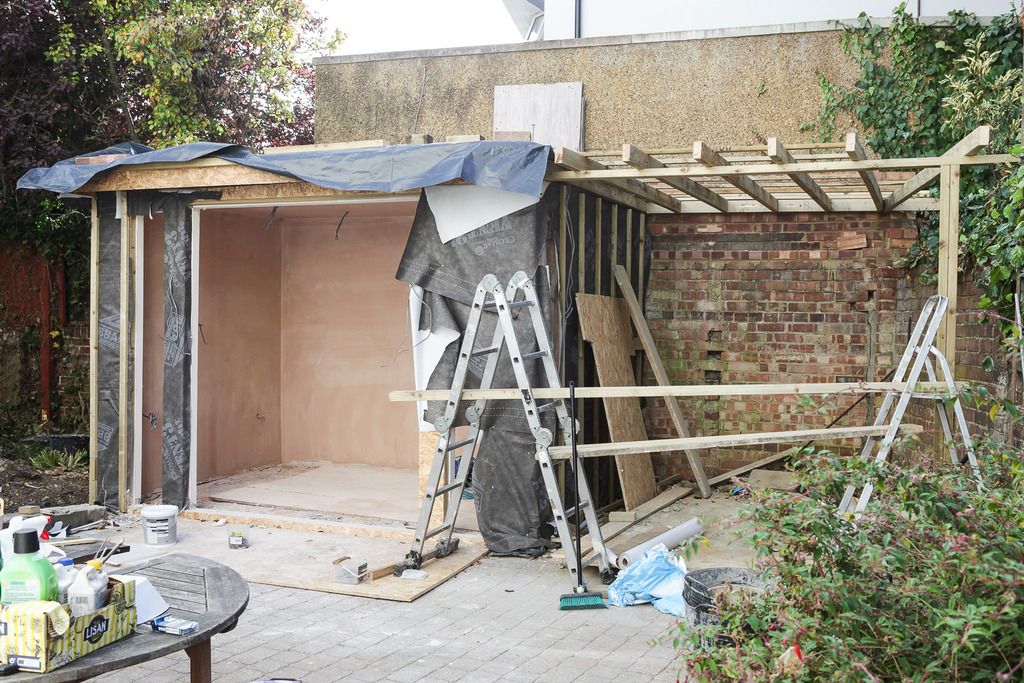
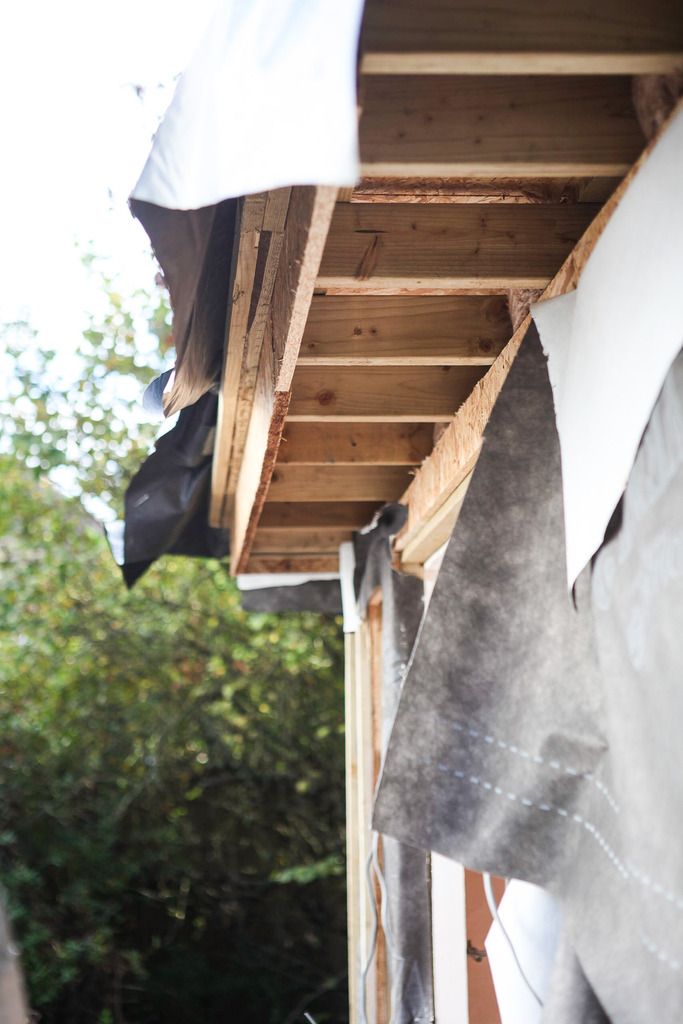
They builders have now abandoned work and left me to it and I have these main problems to address:
1 - The roof is leaking, and the flashing at the rear wall is appalling.
2 - The pre-existing concrete base, which is the floor of the current room, is uneven with a 6cm discrepancy in heights.
3 - Doors and windows need to be measured up and installed
4 - The OSB is left unclad in places, and seems to be interior grade OSB anyway.
5 - The wiring is behind plaster and unlabelled so will need to be identified.
1 The builder laid 50 or 60cm rolls of CORTEX EPDM membrane system by OBEX UK. It's used for lining frames, etc, not roofs. The primary advantage of EPDM for flat roofs is that it can be laid in one sheet with no seams or join. This mess is full of creases, wrinkles, unsealed overlaps and the rear is just loosely laid on lead flashing. It’s not even bonded down, so rain is streaming through the roof.
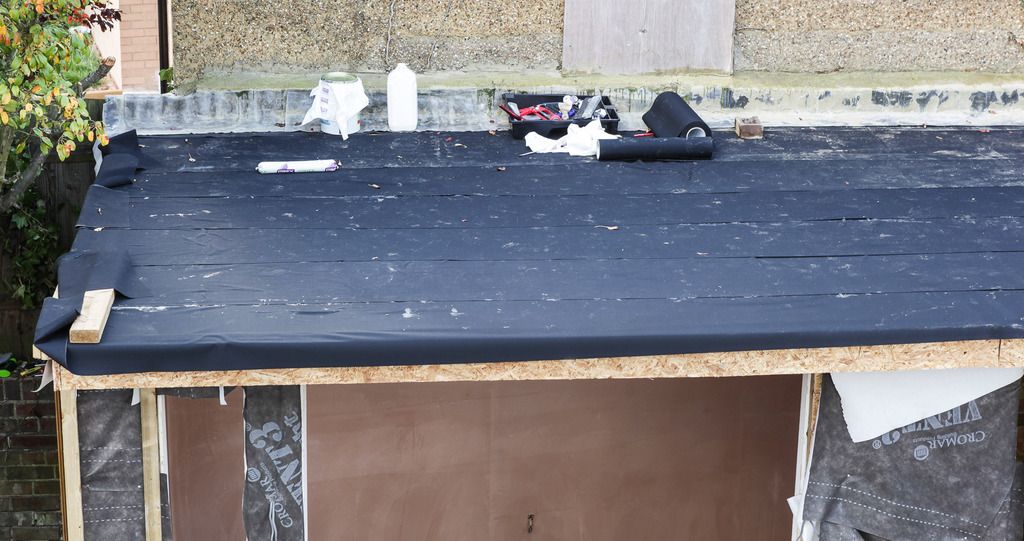
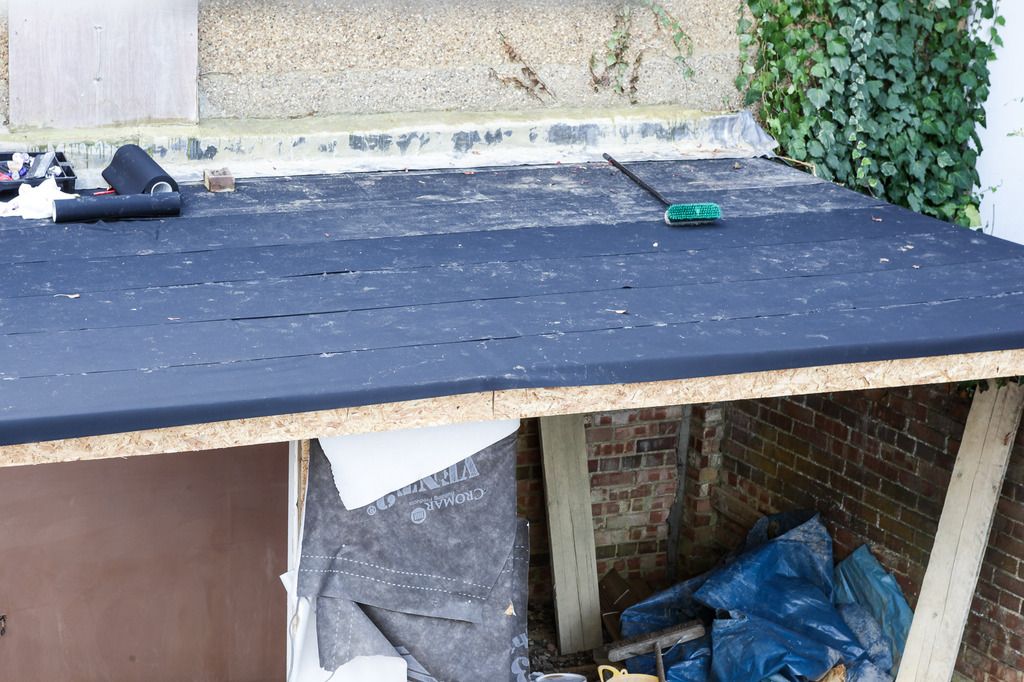
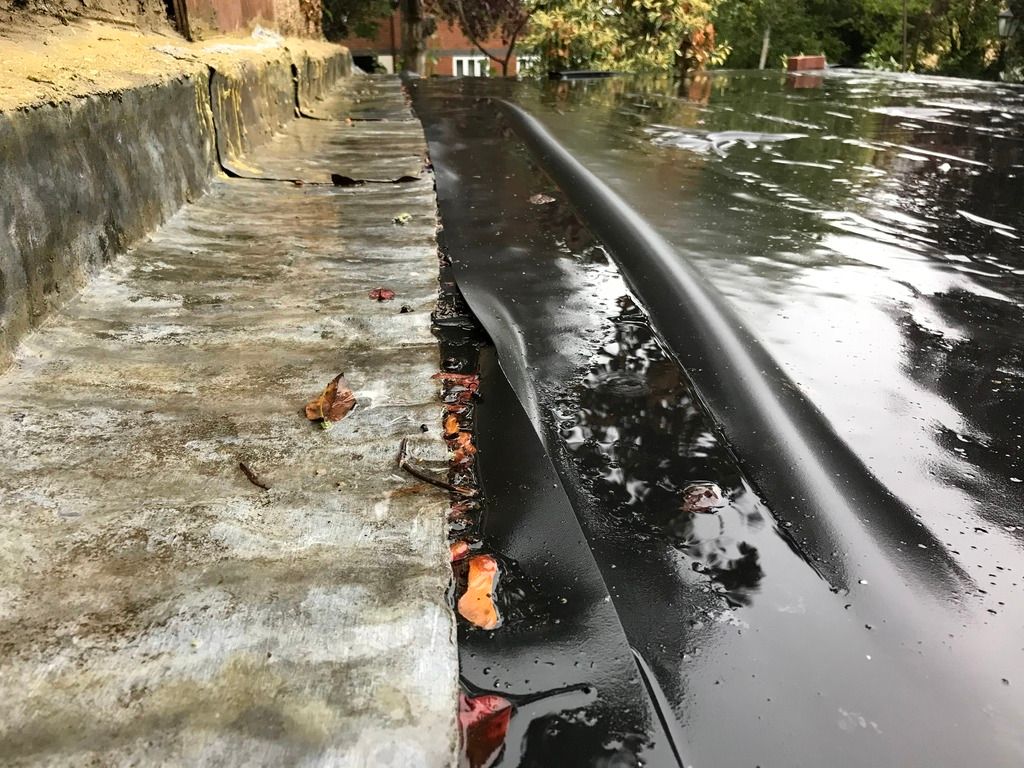
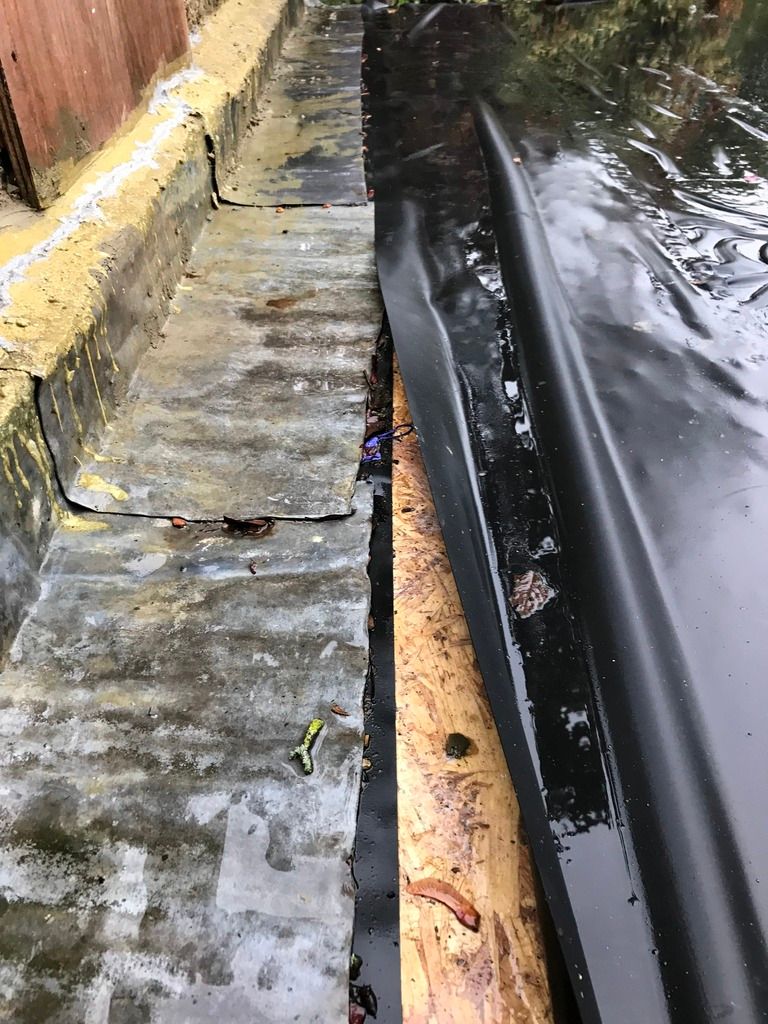
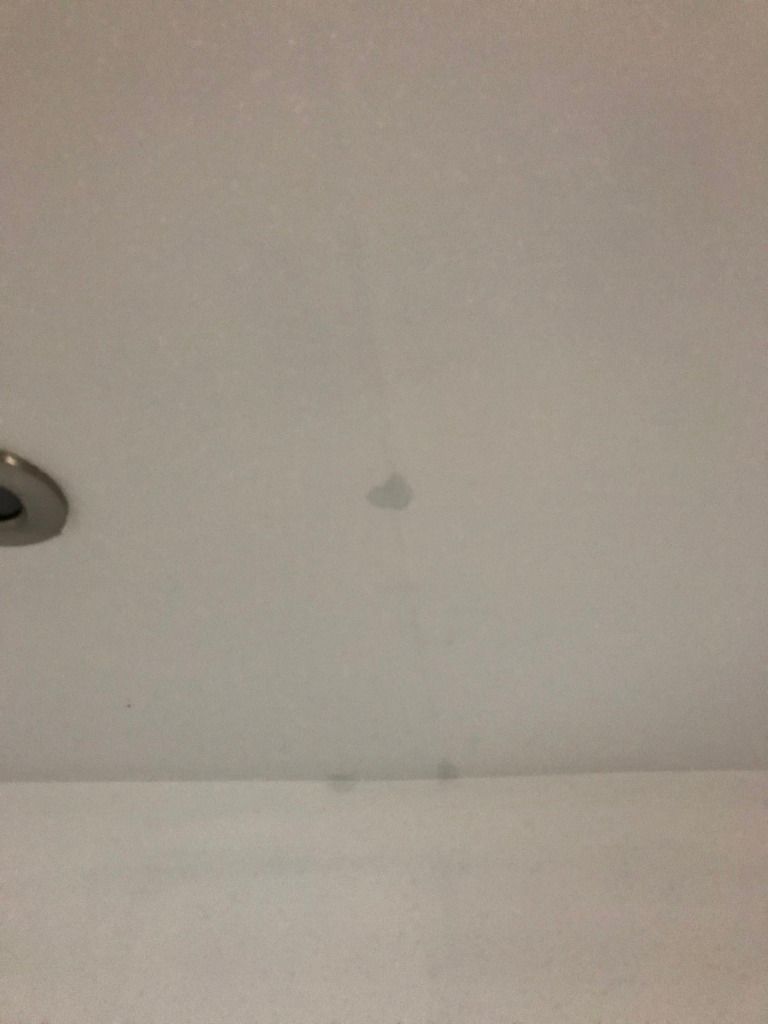
What I need to know is the simplest way to weatherproof this. I thought I might just be able to overlay it with a single sheet of proper epdm, but I believe it doesn’t bond to itself, or is not recommended, so I have to explore other options. Maybe tape to bond down all the seams. Probably redo the flashing so the rubber is chased into the wall behind. Perhaps it’s possible to just physically secure a sheet of epdm over the whole roof and just pin it all the way around the fascia without necessarily bonding it down? Failing that I would just be forced to rip it up and do the whole thing again. Potentially difficult, messy and more expensive. Or I could maybe over board it and do a new roof with better pitch?