He absolutely MUST get a tester that can download it's results, the manual recording is what takes the most time so downloading the results from that many is important.
Odd you say that, I found the reverse, had my own Robin and works Robin PAT tester and the works was all singing dancing model and mine was manual.
The works unit first tested the supply, so every time you unplugged it the test was done again, the readings need to settle, so there are minimum times for each test, so for it to run through the sequence with a class I items it was around 2.6 minutes, does not sound long, but I was dropped off at a remote hub to do PAT testing so thought lets go for it and see how fast I can do it, I had loads of time before I would be picked up again, but just wanted to see how fast, and I was shocked to see it took 4 minutes a test on average.
So maximum for 8 hour day was 120 items, in real terms looking at 100 items by time it has been unplugged and plugged in again. However with my own PAT tester I could beat that, as I can see when needle has settled so each test faster, and with items like a computer I can enter same results for lead set and computer were with the auto one had to test twice for it to log two sets of results.
The other problem was some one fiddling the results, it recorded the results onto floppy disk, and it used VB, the user had to enter his code, which would result in his name on the print out, but there was no option to then remove the code, without entering another, so we had a code called unidentified that we could enter once we had finished, but every so often some one would forget to enter his code, I realised it was using VB so wrote a short program so I could correct errors when some one forgot to enter their code, however the foreman was caught changing the dates on entries and claiming the items had been re-tested when they had not, so keeping computer records was no good, they all had to be printed and the sheets signed, OK the short print so around 60 items per sheet, but we could not rely on computer records.
The PAT tester would auto select the tests required once the plant number was entered, I came to test a mag mount drill, the drill was class II, the mag mount was class I and it seems it had been tested as all class II for years, so having the data in the PAT tester high lighted an error which other wise could have been missed.
But to plug items in we had a case full of adaptors, 16 amp 110 and 230 volt, 32 amp with change over switch to test all three phases, 5 amp round pin, 15 amp round pin later found an adaptor the ones we tell everyone else are dangerous and should be binned as no fuse or shutter.
But the hand drier was a problem, we had to isolate so much to be able to remove the FCU front, then it needed disconnecting, and some supply found for the PAT testing machine, these
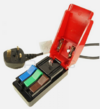
are handy for testing items without a plug, but running an extension lead into the toilets was not really the best option to test a hand drier bolted onto the wall, we did them during the holiday week and two electricians were needed to get around the lone working rules, in fact when testing the batching plant it was three electricians for two days for one item, try covering that with a price per item.
This is why I would say PAT testing needs to be in the main restricted to items with a 13 amp plug, yes the inspection and testing of in service electrical equipment covers it all, but there are problems with some items.
Even a frost free freezer or washing machine can cause problems, and anything else with an auto cycle of events, if for example you have a de-frost element your not going to wait for 8 hours for the defrost cycle to kick in, testing neutral to earth will often show faults, but it depends on how that freezer is controlled, so washing machines, tumble driers, frost free freezers and the like, better to have a maintenance contact so the person testing understands the appliance, specially with things like central heating boilers, as some times one needs to be gas safe to remove covers.
The English law for EICR in rented property seems to expect the installation to include any items not readily moved, and it seems they expect the guy doing the EICR to include the immersion heater, however really that is not part of the installation, that is equipment so comes under PAT testing, however unlikely to test it with a PAT testing machine, it is get the installation tester out.
So many places I worked it was agreed that some items would be tested when we did the EICR, OK the results would be recorded in the PAT testing records not the EICR, but they would not be tested using a PAT tester.
The job needs carefully defining, or items can be missed out, it is fine saying hand drier tested when doing the EICR, as long as the guy doing the EICR knows he needs to test it.