- Joined
- 28 Aug 2016
- Messages
- 2
- Reaction score
- 0
- Country
Hi,
I wanted to replace a few small, trouble, type 11 rads for some new type 22 ones to give a little more output in the winter months. I have 10mm copper pipework that comes out of the wall, so I was fully prepared to have to unsolder and extend it to take into account the extra width and larger stand-off. The house is 15 years old and as far as I am aware, has had no work done on these rads since it was built.
I removed one of them and found that the copper tails seemed more free to move than I would have expected. I popped an endoscope in next to the pipe and saw what looked like a pushfit, just 100mm along the copper, concealed between the blockwork and plasterboard.
When soldering these sorts of pipes, I normally use a wet rag or heat block as a precaution, however I am fairly certain that at this distance, the plastic/rubber would be destroyed anyway.
Unsure how to approach this, I decided to cut out a section of plasterboard to see exactly what I was dealing with (see pictures). I have a handful of these to do, so I figured if I make a mess on one, at least I know where I stand. A short investigation on some of the others, seems to yield the same results. Concealed pushfits a short distance from the copper, sandwiched between the plasterboard and blockwork and sometimes covered over by plasterboard adhesive (thanks for making my life easy mr house builder).
So... How do you suggest I approach this? Is this normal practice for house builders?
My only thought is to cut out the plaster up to the pushfit, remove it, install new copper to the rad, replace and reconnect with a new pushfit, then repair the damaged plasterboard.
Seems a lot of work just to replace a rad, so was hoping someone with a little more experience might have an idea.
Thanks.
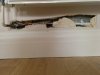
I wanted to replace a few small, trouble, type 11 rads for some new type 22 ones to give a little more output in the winter months. I have 10mm copper pipework that comes out of the wall, so I was fully prepared to have to unsolder and extend it to take into account the extra width and larger stand-off. The house is 15 years old and as far as I am aware, has had no work done on these rads since it was built.
I removed one of them and found that the copper tails seemed more free to move than I would have expected. I popped an endoscope in next to the pipe and saw what looked like a pushfit, just 100mm along the copper, concealed between the blockwork and plasterboard.
When soldering these sorts of pipes, I normally use a wet rag or heat block as a precaution, however I am fairly certain that at this distance, the plastic/rubber would be destroyed anyway.
Unsure how to approach this, I decided to cut out a section of plasterboard to see exactly what I was dealing with (see pictures). I have a handful of these to do, so I figured if I make a mess on one, at least I know where I stand. A short investigation on some of the others, seems to yield the same results. Concealed pushfits a short distance from the copper, sandwiched between the plasterboard and blockwork and sometimes covered over by plasterboard adhesive (thanks for making my life easy mr house builder).
So... How do you suggest I approach this? Is this normal practice for house builders?
My only thought is to cut out the plaster up to the pushfit, remove it, install new copper to the rad, replace and reconnect with a new pushfit, then repair the damaged plasterboard.
Seems a lot of work just to replace a rad, so was hoping someone with a little more experience might have an idea.
Thanks.
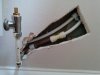
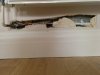