Could do with some advice here.
The problem- timber floor a bit tatty, weak spots in the bays by the chimney breast, usual stuff.
Lifted some floorboards to find zero void beneath the joists which were supported on random bits of brick. Joists in surprisingly good nick (3" x 2" old fine-grained, pretty straight, some of the tails rotted out).
Exploratory dig found the bottom (soldier course) of the front wall (no concrete underneath) at about 450 below ffl (that to the top of the soldiers).
So plan was dig out the rubble and some clay to get down to about 450mm below ffl, this leaving room for 50mm sub base, 200mm void, 45 x 170 joists with 200mm rockwool between them (held up with pvc netting).
Annoyingly, the other walls have shallower footings, the worst one being the spine wall with top of soldiers at about 250 below ffl.
Annoyingly 2 the clay is very hard so tends to come out in chunks so its been almost impossible to just leave a 45° slope of undisturbed clay near the wall- so for now there's a 300mm wide strip of undisturbed clay along most of that wall which tops out at about 190 below ffl.
Given all that, the next bit of the dig (going down to 600 below ground for footings for dwarf walls) seems unwise. So contemplating alternatives;
1 Floating floor- concrete to 140 below ffl, dpm, 100mm pir, t & g loft boards glued then t & g floorboards nailed on top.
2 Half breed floor- concrete to 250 below ffl then dpm then concrete to 200 below ffl then 45 x 150 joists on dwarf walls (to give room for insulation & reduce thermal bridging) then t & g floorboards on top. No ventilation to timbers- have read that this is OK but i can't remember where. Possibly on here somewhere..
With either of the above, will i be better off leaving the clay next to the spine wall or digging it out to expose the bricks?
3 Carry on with suspended floor, set dwarf walls on top of the subfloor, work round the high ground level bit.
4 Raise FFL by 100mm - would rather not have a step from hallway into library but worse things happen at sea.
5 As it happens I could raise FFL (or more accurately not floor above that 300mm wide clay strip on the spine wall)- plan for that wall is all bookshelves so it starting 150 above ffl would not be a problem.....
Sorry for long and wordy post, there are some pics to follow.
My thinking behind both above sketches is pouring a decent chunk of concrete directly against the brick walls will give a bit of friction reinforcement to the walls and a bit of resistance to ground heave. I really don't want to start underpinning the (full brick) spine wall- i can't afford to get it done professionally and i'm not confident i'd be able to DIY it successfully.
Any suggestions gratefully received. Except the ones that say knock it down and start again or bodge it and flog it.
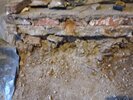
Comedy constructional hearth. Shame cos the tiles on top were in reasonable nick.
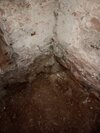
Chimney breast (on left) soldiers at about 450 below. Wall on right starts at about the same depth
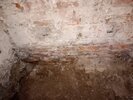
But then comes up a course so soldier top now 350 ish below
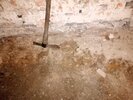
Spine wall- right hand end of mattock level with bottom of soldier at 350 ish below, top of soldier 280 ish.
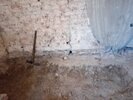
Don't know what is under that strip of clay but i'm sure it won't be pretty. Leaving it well alone, possibly for ever, possibly til an hour before the concrete pour for floating or halfbreed floor.
The problem- timber floor a bit tatty, weak spots in the bays by the chimney breast, usual stuff.
Lifted some floorboards to find zero void beneath the joists which were supported on random bits of brick. Joists in surprisingly good nick (3" x 2" old fine-grained, pretty straight, some of the tails rotted out).
Exploratory dig found the bottom (soldier course) of the front wall (no concrete underneath) at about 450 below ffl (that to the top of the soldiers).
So plan was dig out the rubble and some clay to get down to about 450mm below ffl, this leaving room for 50mm sub base, 200mm void, 45 x 170 joists with 200mm rockwool between them (held up with pvc netting).
Annoyingly, the other walls have shallower footings, the worst one being the spine wall with top of soldiers at about 250 below ffl.
Annoyingly 2 the clay is very hard so tends to come out in chunks so its been almost impossible to just leave a 45° slope of undisturbed clay near the wall- so for now there's a 300mm wide strip of undisturbed clay along most of that wall which tops out at about 190 below ffl.
Given all that, the next bit of the dig (going down to 600 below ground for footings for dwarf walls) seems unwise. So contemplating alternatives;
1 Floating floor- concrete to 140 below ffl, dpm, 100mm pir, t & g loft boards glued then t & g floorboards nailed on top.
2 Half breed floor- concrete to 250 below ffl then dpm then concrete to 200 below ffl then 45 x 150 joists on dwarf walls (to give room for insulation & reduce thermal bridging) then t & g floorboards on top. No ventilation to timbers- have read that this is OK but i can't remember where. Possibly on here somewhere..
With either of the above, will i be better off leaving the clay next to the spine wall or digging it out to expose the bricks?
3 Carry on with suspended floor, set dwarf walls on top of the subfloor, work round the high ground level bit.
4 Raise FFL by 100mm - would rather not have a step from hallway into library but worse things happen at sea.
5 As it happens I could raise FFL (or more accurately not floor above that 300mm wide clay strip on the spine wall)- plan for that wall is all bookshelves so it starting 150 above ffl would not be a problem.....
Sorry for long and wordy post, there are some pics to follow.
My thinking behind both above sketches is pouring a decent chunk of concrete directly against the brick walls will give a bit of friction reinforcement to the walls and a bit of resistance to ground heave. I really don't want to start underpinning the (full brick) spine wall- i can't afford to get it done professionally and i'm not confident i'd be able to DIY it successfully.
Any suggestions gratefully received. Except the ones that say knock it down and start again or bodge it and flog it.
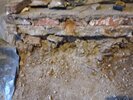
Comedy constructional hearth. Shame cos the tiles on top were in reasonable nick.
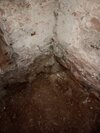
Chimney breast (on left) soldiers at about 450 below. Wall on right starts at about the same depth
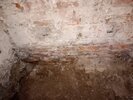
But then comes up a course so soldier top now 350 ish below
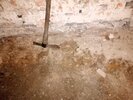
Spine wall- right hand end of mattock level with bottom of soldier at 350 ish below, top of soldier 280 ish.
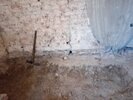
Don't know what is under that strip of clay but i'm sure it won't be pretty. Leaving it well alone, possibly for ever, possibly til an hour before the concrete pour for floating or halfbreed floor.