Thought this might be a good place to ask this. I'm building a scissor lift for my garage, capable of lifting 200kg ish. I bought a 24v hydraulic pump and was going to buy a ram and pendant remote. However I've just come across an electric linear actuator capable of lifting 300Kg. Its a gate opener but should work. It will be much neater, quieter, lighter, cheaper and hopefully less hassle.
I've seen how to wire up an actuator with 2 wires to a rocker switch but the actuator I'm looking at has 4 wires. I'm trying to get my head around the 'common' wire.
Is this diagram below how the actuator would be wired up or am I nowhere near?
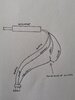
I've seen how to wire up an actuator with 2 wires to a rocker switch but the actuator I'm looking at has 4 wires. I'm trying to get my head around the 'common' wire.
Is this diagram below how the actuator would be wired up or am I nowhere near?
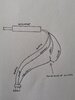