Hi all,
I have the following project lined-up and would greatly appreciate some advise/input on a couple of points.. :
The room in question
We have a porch/utility/outhouse attached to the front of the house (see pic below).. It has a built-up felt flat roof, single-skin +/-95mm thick (half brick?) walls on three sides, a concrete/screed floor, and is not heated by the main house CH system.
The three single-skin walls do have an integral DPC (visible in the first photo, level with the base of the door cill).
There are two doors.. one is the front door (seen in the pic) and the other is inside and leads from the 'outhouse' inside to the dowstairs hallway. The house is an early 70s terrace.
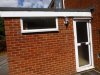
Current make-up inside
The roof is a 'cold roof' so has a plasterboard ceiling with loft-style insulation half-filling the (ventilated) cavity between the rafters/joists beneath the boards.
The walls are currently lined with dot-n-dab fixed plasterboard (probably done in the late 80s-early 90s).
The floor currently has a thin underlay beneath some cheap laminate flooring..
Present issues
The flat roof is old and has leaked in the last couple of months.. (I've made a temp/patch repair in the meantime). The old-style coated chipboard boards are showing signs of failure..
The plasterboard ceiling is failing in places and the boards starting to droop..
The plasterboard dabs have mostly detached from the walls.
My intentions
I intend to have a roofer strip, re-board and re-felt the roof (still a 'cold roof' construction).
I intend to replace the roof insulation with 75mm Celotex and re-line the ceiling.
I intend to re-line the walls and thought best to add some form of insulation whilst the opportunity presents itself as I understand (although unheated) something is better than nothing..
I am not planning to insulate the floor, the laminate flooring will likely be replaced with carpet.
The room will remain unheated and detached from the main house CH.. at best, it will have a portable/panel heater to take the chill-off if/as/when required.
I am yet to finalise which method to use when insulating the walls.. whether to have conventional PIR insulation boards between studwork then p/b over and skim to finish; or, to batten the walls and fix thermal laminate p/b and skim to finish..
My question is..
Having removed some of the existing plasterboard from the walls, I can see the walls have been painted with what looks like a liquid DPM in the past (see pics).
Regarding this coating, should I..
a) try to remove it in order to leave a 'permeable' wall?;
b) leave it as it is?;
c) add something similar (like BlackJack liquid DPM) over the top..?
The application guidance from Celotex for the internal insulation of solid walls seems to suggest that the wall should be permeable and stripped/clear of coatings. I am reading elsewhere that either a liquid DPM or a plastic sheet/tanking should be in-place..?
Is the guidance from Celotex based on the assumption that the solid wall is a double-brick-width thickness and not prone to ingress from the outside..?
Many thanks in advance of any thoughts/input you can offer..
Apologies to ramble on.. I tried to keep it short..!
I have the following project lined-up and would greatly appreciate some advise/input on a couple of points.. :
The room in question
We have a porch/utility/outhouse attached to the front of the house (see pic below).. It has a built-up felt flat roof, single-skin +/-95mm thick (half brick?) walls on three sides, a concrete/screed floor, and is not heated by the main house CH system.
The three single-skin walls do have an integral DPC (visible in the first photo, level with the base of the door cill).
There are two doors.. one is the front door (seen in the pic) and the other is inside and leads from the 'outhouse' inside to the dowstairs hallway. The house is an early 70s terrace.
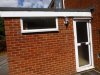
Current make-up inside
The roof is a 'cold roof' so has a plasterboard ceiling with loft-style insulation half-filling the (ventilated) cavity between the rafters/joists beneath the boards.
The walls are currently lined with dot-n-dab fixed plasterboard (probably done in the late 80s-early 90s).
The floor currently has a thin underlay beneath some cheap laminate flooring..
Present issues
The flat roof is old and has leaked in the last couple of months.. (I've made a temp/patch repair in the meantime). The old-style coated chipboard boards are showing signs of failure..
The plasterboard ceiling is failing in places and the boards starting to droop..
The plasterboard dabs have mostly detached from the walls.
My intentions
I intend to have a roofer strip, re-board and re-felt the roof (still a 'cold roof' construction).
I intend to replace the roof insulation with 75mm Celotex and re-line the ceiling.
I intend to re-line the walls and thought best to add some form of insulation whilst the opportunity presents itself as I understand (although unheated) something is better than nothing..
I am not planning to insulate the floor, the laminate flooring will likely be replaced with carpet.
The room will remain unheated and detached from the main house CH.. at best, it will have a portable/panel heater to take the chill-off if/as/when required.
I am yet to finalise which method to use when insulating the walls.. whether to have conventional PIR insulation boards between studwork then p/b over and skim to finish; or, to batten the walls and fix thermal laminate p/b and skim to finish..
My question is..
Having removed some of the existing plasterboard from the walls, I can see the walls have been painted with what looks like a liquid DPM in the past (see pics).
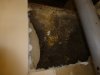
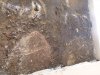
Regarding this coating, should I..
a) try to remove it in order to leave a 'permeable' wall?;
b) leave it as it is?;
c) add something similar (like BlackJack liquid DPM) over the top..?
The application guidance from Celotex for the internal insulation of solid walls seems to suggest that the wall should be permeable and stripped/clear of coatings. I am reading elsewhere that either a liquid DPM or a plastic sheet/tanking should be in-place..?
Is the guidance from Celotex based on the assumption that the solid wall is a double-brick-width thickness and not prone to ingress from the outside..?
Many thanks in advance of any thoughts/input you can offer..
Apologies to ramble on.. I tried to keep it short..!