Hi
Hoover started labouring. The brushes were worn enough to see a copper wire in the end. I replaced the brushes but the motor still doesn't sound right. I can also see some arcing when the motor runs but I don't know if that was there before.
A couple of commutator segments are more carbon coated than others and you can also see the new brushes have chipped!
Any idea what's going on? Defective brushes? Do I need to clean the commutator? Is it worth it or do I buy a new motor?
Thanks
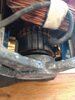
Hoover started labouring. The brushes were worn enough to see a copper wire in the end. I replaced the brushes but the motor still doesn't sound right. I can also see some arcing when the motor runs but I don't know if that was there before.
A couple of commutator segments are more carbon coated than others and you can also see the new brushes have chipped!
Any idea what's going on? Defective brushes? Do I need to clean the commutator? Is it worth it or do I buy a new motor?
Thanks
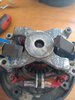
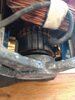
Last edited: